Ice machines are indispensable in various settings, from restaurants and cafes to office break rooms and households. They provide the convenience of ice on demand, which is essential for beverages and culinary preparations.
However, like any frequently used appliance, ice machines can encounter issues affecting performance and output. Fixing an ice machine might seem daunting, but with the proper knowledge and tools, you can troubleshoot common problems.
Here, we unveil expert secrets on how to fix an ice machine, ensuring your appliance runs smoothly and efficiently.
5 Expert’s Secrets on Fixing Ice Machines
We’ve got professional trade tips on how to get your ice machines run smoothly again.
- Understanding the Basics
Before attempting any repairs, familiarize yourself with your ice machine’s essential operation and components. Most ice machines fill a freezing tray with water, freeze it into ice, and then release it into a storage bin.
The water inlet valve, evaporator, thermostat, and ice mold are vital components. Identifying these parts will help you diagnose issues more accurately.
- Regular Cleaning and Maintenance
Regular cleaning and maintenance is one of the most crucial yet often overlooked aspects of keeping an ice machine in top condition. Mineral buildup from hard water can clog water filters and lines, affecting ice quality and production.
Experts recommend cleaning your ice machine every six months with a nickel-safe cleaner and sanitizer to remove scale and microbial growth. Always refer to the manufacturer’s instructions for the recommended cleaning procedure.
- Troubleshooting Common Issues
Let’s look at the common issues behind non-functioning ice machines.
- No Ice Production
If your ice machine stops producing ice, check if it receives power and the water supply is on. Next, inspect the water inlet valve for blockages or malfunction; a defective valve can prevent water from entering the ice mold.
Additionally, a faulty thermostat might not trigger the freezing cycle, necessitating a replacement.
- Poor Ice Quality
Cloudy, minor, or oddly shaped ice can indicate water filtration or flow issues. Replace water filters regularly to ensure clean, clear ice.
Also, check the water inlet valve and lines for any restrictions limiting water flow to the ice mold.
- Ice Not Ejecting
If ice forms but does not eject into the bin, the issue might be with the heating element that warms the bottom of the ice mold, allowing the ice to release. A malfunctioning heating element or control module that doesn’t activate the heating cycle will require replacement.
- Electrical Component Care
When working with electrical components like thermostats, heating elements, or control modules, ensure the power is completely off before starting any repairs. Use a multimeter to test electrical parts for continuity.
If you’re unfamiliar with handling electrical components, consult a professional to avoid injury or further damage to the machine.
- Seek Professional Help When Necessary
While many ice machine issues can be resolved with basic troubleshooting, some problems require expert attention. Complex cases involving refrigerant levels or sealed system repairs are best left to certified technicians with the tools and training to handle these tasks safely and effectively.
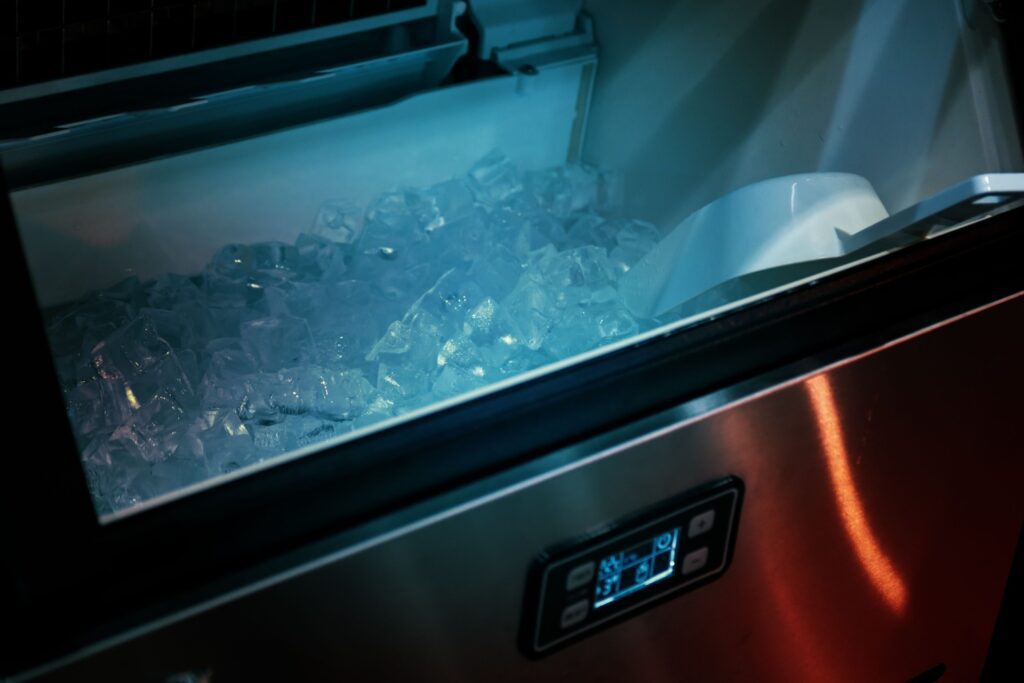
Professionals Are on Standby to Help with Your Ice Machines
Fixing an ice machine involves identifying the root cause of the problem, regular maintenance, and, sometimes, replacing faulty components. By following these expert secrets, you can extend the life of your ice machine and ensure it continues to produce high-quality ice.
However, remember that when in doubt, consulting with professionals such as A-Tech Repair is the safest and most effective way to address complex issues.
If you have any questions about HVAC systems or queries about installations or repairs, contact A-Tech Appliance Repair, who will gladly assist.